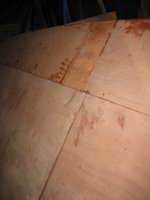


I was mixing up a batch of epoxy glue to join the upper hull panel to the lowers when I looked up - it was snowing. A quick check of both the shed and my indoor/outdoor thermometers showed that it was 5 degrees above freezing. What was going on? Suddenly I had a new concern, if this snow stuck around could the shed roof handle the snow load? Despite bizarre weather with high humidity and cool temperatures, I continue building. I stewed over the long weekend about how the upper panels were landing on the completed hull. The first issue was that the upper panels could have been 1/4 inch wider as in 12.25 inches instead of 12 and would line up better with the bulkheads and cabin sides. The reason for this is a result of the difficulty in getting the bulkheads all the way to the bottom of the lower hull panels when you first push then into the wired together hull. My advice - insert a pencil between the wire and the keel when you stitch the hull together at the keel to lower panels joint. This way you will get enough slack in the wires to properly open them up. I could have "corrected this problem at the top of the bulkheads by not overlapping the upper to lower sides by a full inch but this is an important joint. The inch is a minimum I feel. The second issue was way more critical to me. The longitudinal panel joints where landing too close together, separated by only a couple of inches. To fix this meant undoing several days work, figuring out how to modify the upper panels to shift the lower and upper joints apart (see before and after photos in this post) and then making it happen. As I had already drilled holes for the screws and I wanted to reuse these, I had to figure out how much to shift the upper panel so the screw holes lined up (luckily I'd laid them out on regular centers at 25 cm), the backing blocks didn't land at the bulkheads and that I could add a new section from the scrap I had on hand. The measurement turned out to be 1012mm. I drew the line and then stewed some more. I was about to live with it BUT it's a boat, "keep in mind what it has to endure when it is in a big seaway or worse touches bottom as you sail in shallow waters - think of the stress." In hadn't fully removed the panel. All I had done was roll the boat on its side (no small feat) on sawhorses, undone the necessary screws at the bow, raised the upper panel away from the lower with an inserted two by four and marked the cut line. I checked my measurements once more, stewed some more and plugged my panel saw in. What a load of work I was creating for my self! I still wasn't ready to make the cut - I could just forget it, it wouldn't be an issue but my conscious kept at me. I went inside for another look at the plans, Wharram doesn't offset the panels much, maybe a foot I said to myself - an inch a foot what's the difference. I checked Sam Devlin's book, Devlin's Boatbuilding - he didn't have much to say on offsetting panels but what I kept hearing was a conversation I'd had many years ago with John Lockwood of Pygmy Kayaks about offsetting panels for strength of the joint. If the panels line up the joint can "zipper" open. Spread the strain. It makes total sense afterall, that is what you do in any shear panel. Stew, stew and stew! Then I thought about old time boatbuilders who supplied the local village with their boat needs. That kind of boatbuilder stayed in business by the success of the product. If the boats didn't return from there voyages then maybe the mariners in that village would seek out a boat elsewhere. In the modern world of commercial boatbuilding this effect is somewhat lost. There is little connection between the users and the producers - it creates a "can't see it from my house" environment. Back to the shed. I picked up the panel saw pressed down the trigger and ten seconds later was feeling much better.
With the bow a little short now, I removed the rest of the screws, moved the panel forward, aligned it, set some nails on the one inch line to get the upper panel to sit right and proceeded to refasten it. I switched from a SS #8 x 3/4" screw to a SS #8 by 1" and worked my way along. At the stern I made a kraft paper template of the piece I needed leaving the old angled stern as it was. After making the template I found a suitable piece of scrap, cut out a new piece and suitable backing block and screwed these to the hull. I wired the top edge to the bulkheads and inner sheer clamp (mis-named earlier as deck clamp), put a temporary 1 x 2 on the outside to get the curve right and stood the whole thing back on its keel. After all the stewing about having to go backwards days of work, the correction took no more than two or three hours. The lesson learned, again!, if the work you've just done doesn't sit right with you, do it again until it's right. You won't worry about it failing when you are in a tough spot bouncing around in the slop.
0 Comments:
Post a Comment
<< Home