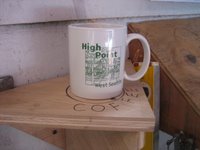
This isn't the first time I've posted a picture of my coffee cup. The last time I was celebrating my new dedicated coffee shelf and talked about the importance of creating the environment necessary to keep at it and with it to the end (Post October 14th). How many partly finished boats fill driveways, carports and backyards? Why did these dreams begin with such enthusiasm only to be abandoned? Building a boat is a big deal. Building a catamaran is even bigger. You will have two hulls to compare. The first one may perhaps not be as great or nice as the second one. Will you have to build a third? The size of boat you choose is a big factor. As length increase linearly, volume does so cubicly. Consider volume as the true gauge of construction cost and time. Who has months upon months if not years to build a boat. Who has the tools, the shop space the gantry crane, if the boat is really big, to complete such an undertaking not to mention the money. I think the Tiki 26 or perhaps a Pahi 31 should be the biggest project you set out on in your backyard and as your first Wharram stitch and glue tortured plywood construction. If I ever take on a bigger one, I'll hire help and build in a proper work building with some kind of overhead lift. I'm still not sure how I will maneuver the first tiki 26 hull out of my shed once it is complete - all 430 pounds of it. If you have never built a boat this way and if you were looking for my advice and you wanted to tackle a big one, I'd give the following "consider the first step in your adventure to be the building of a Hitia 14 or 17. What you will learn will be invaluable and you will have something to sail while you are building the real boat so you can refresh your motivation and regain focus. It will be cheaper than the partly finished hull in your driveway that keeps nagging at you." But wasn't I talking about coffee cups!
Before I started building my Tiki 26, I took the summer off to decompress. I find myself very lucky in that I successfully escaped from an extremely stressful job. The coffee cup is a remnant of the $120 million project, High Point in West Seattle, I was in charge of building. When I discovered that I no longer had a life, I knew it was time to leave. The message was clear - No time to sail is no life! But how? Though I escaped, I didn't do it in one step as I got sucked into another "dream project" and managed to get that project underway before I woke up and realized I was going down the rabbit hole again and needed to pass the project on. Circumstances and the right opportunity let me slip out the door before I was sucked in deep. But somehow I wasn't getting the message as early as I should have. Everytime I would go for an annual checkup, my doctor would remind me that construction project management of the multimillion dollar projects that I get hired to run is not the best for your health. What did it was when I found myself yelling at a woman who was letting my daughter walk her dog (the dog was walking my daughter out on to the road from a school playground). This made me realize that it was time to step back. The issue was real but my response was over the top. I made a plan, figured out how to set aside enough to live on and said to myself, at this point in time what do you really want to do? The answer didn't come easy. At first it was do nothing, then do everything. Then it narrowed to two boat plans and one non-boat thing. As I decompressed over the summer my head cleared and by the middle of July I was focused on the two boat things. I took the further step of buying plans for the Tiki 26 (Plan A) while I still looked for a boat to buy and refit for a round the world sail (Plan B). By late August, I was studying the Tiki plans intently and figuring out costs and schedule.
So now I am here. In a sense, I am doing what I was doing before but now I love it whereas before I didn't. Building versus building. And why do I hear from so many who when they see what I am doing share with me their work traumas and dislikes. Why do we do things we don't like or don't want to do? Why don't we follow our dreams? The easy answer is that we need to earn money to live on or support our families with but these are poor answers in the end as we may be alive but we are not living. To be alive, truly alive we must throw fear out, stop doing what we think is right and set course steering by our dreams not our dreads!